It is possible to supply ATV930 by external DC supply. The most simple calculation for DC supply voltage is to multiply ATV's AC input voltage range by sqrt(2) and you will get the DC bus voltage that ATV needs.
For example if ATV930..N4 allows AC supply 380..480V, then adequate level of DC bus is 1.41*380...1.41*480 which is 537...678V DC.
There is one more aspect to be considered, though. Motor rated voltage. As you know, ATV output voltage cannot be greater than input AC voltage, therefore bear in mind that Dc bus voltage should no be lower than sqrt(2)*rated motor voltage.
If your motor rated voltage is 400V, then DC bus voltage should be at least 565V.
So for 400V motor, the optimal level of DC bus voltage is 565V or little bit higher.
Next, ATV drives (ATV61-71, ATV process) up to 18.5kW have built-in pre-charging resistor that will limit pre-charging current, so direct connection to external DC supply is possible.
But the drives from 22kW and above do not have pre-charging resistor. Their charging current is limited by thyristors in ATV input rectifier when they are supplied by input AC voltage. But here with external DC supply there is nothing in ATV to limit the current. Therefore any drive above 22kW that is supplied by external DC voltage requires external pre-charging circuit. The circuit can compose of resistor + bypass relay(or contactor). The bypass relay may be controlled by ATV relay output assigned to "DC bus charged". See page 440 from ATV930 programming manual NHA80757 02/2017.
Approximate resistance of pre-charging resistor to be calculated by rated DC current (Idc) and DC supply voltage (Udc).
R=Udc/Idc.
Select resistor with resistance 0.8*R ... 2*R. (Value lower than 80%R will affect capacitor lifetime, and too high resistance will prolong pre-charging time)
Rated DC current is Idc_n=P_n/Udcmin where P_n is rated ATV power and Udcmin is minimum required DC voltage (1.41*380V in case of ATV930..N4).
During external DC supply design, consider DC current as P/Udc, where P is drive power and Udc is DC bus voltage provided by external DC supply. Regarding drive power P , consider either drive rated power (when application does not require overload) or include short time overload as specified in selected drive datasheet, for example continuous drive power P = rated motor power and short time overload power is :
1.1x rated motor power during 60s for Altivar ATV630 selected for normal duty ND
1.5x rated motor power during 60s for Altivar ATV630 selected for heavy duty HD
1.2x rated motor power during 60s for Altivar ATV930 selected for normal duty ND
1.5x rated motor power during 60s for Altivar ATV930 selected for heavy duty HD
For example if ATV930..N4 allows AC supply 380..480V, then adequate level of DC bus is 1.41*380...1.41*480 which is 537...678V DC.
There is one more aspect to be considered, though. Motor rated voltage. As you know, ATV output voltage cannot be greater than input AC voltage, therefore bear in mind that Dc bus voltage should no be lower than sqrt(2)*rated motor voltage.
If your motor rated voltage is 400V, then DC bus voltage should be at least 565V.
So for 400V motor, the optimal level of DC bus voltage is 565V or little bit higher.
Next, ATV drives (ATV61-71, ATV process) up to 18.5kW have built-in pre-charging resistor that will limit pre-charging current, so direct connection to external DC supply is possible.
But the drives from 22kW and above do not have pre-charging resistor. Their charging current is limited by thyristors in ATV input rectifier when they are supplied by input AC voltage. But here with external DC supply there is nothing in ATV to limit the current. Therefore any drive above 22kW that is supplied by external DC voltage requires external pre-charging circuit. The circuit can compose of resistor + bypass relay(or contactor). The bypass relay may be controlled by ATV relay output assigned to "DC bus charged". See page 440 from ATV930 programming manual NHA80757 02/2017.
Approximate resistance of pre-charging resistor to be calculated by rated DC current (Idc) and DC supply voltage (Udc).
R=Udc/Idc.
Select resistor with resistance 0.8*R ... 2*R. (Value lower than 80%R will affect capacitor lifetime, and too high resistance will prolong pre-charging time)
Rated DC current is Idc_n=P_n/Udcmin where P_n is rated ATV power and Udcmin is minimum required DC voltage (1.41*380V in case of ATV930..N4).
During external DC supply design, consider DC current as P/Udc, where P is drive power and Udc is DC bus voltage provided by external DC supply. Regarding drive power P , consider either drive rated power (when application does not require overload) or include short time overload as specified in selected drive datasheet, for example continuous drive power P = rated motor power and short time overload power is :
1.1x rated motor power during 60s for Altivar ATV630 selected for normal duty ND
1.5x rated motor power during 60s for Altivar ATV630 selected for heavy duty HD
1.2x rated motor power during 60s for Altivar ATV930 selected for normal duty ND
1.5x rated motor power during 60s for Altivar ATV930 selected for heavy duty HD
Released for:Schneider Electric Nigeria
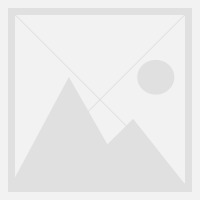
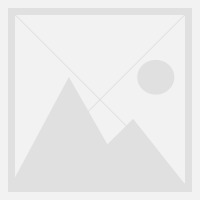
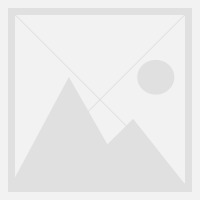
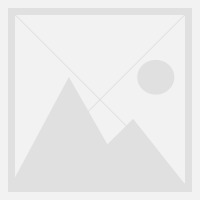
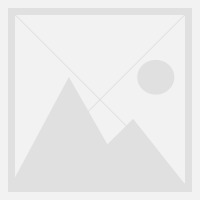
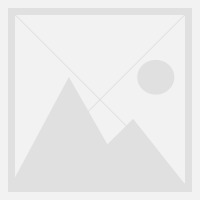