Cumulated quantity of water flown can be provided by Altivar Process ATV600 drive only if there is flow sensor connected to ATV630 drive. If there is not any flow sensor, the pump flow can only be estimated (using flow estimation function) based on defined head vs flow or power vs flow curves.
Bear in mind that estimated pump flow cannot be as precise as measured pump flow (from flow sensor) and therefore estimated pump may give total quantity with significant distortion.
One solution is to read estimated pump flow via PLC and calculate total quantity in PLC.
Other solution is to read SLFV by then PLC to return value by writing it into virtual input (e.g. AIV1). As ATV630 allows to assign pump sensor to virtual input, ATV630 will process it and hence total quantity will be calculated by the drive.
ATV630 needs real pressure sensor in order to estimate flow from H-Q curves. Pump curves must be configured in the drive. Virtual input to be assigned to installation flow and the rest is about the scaling.
Note that value in virtual input has different scaling than read SLFV, so you have to adjust it using virtual input scaling (AVxJ AVxK). Everything explained in attached picture. As an example psx config is attached.
Modbus TCP was used in example, but in principle any other communication is possible.
parameter FS1C that provides Total quantity will be visible also on HMI, in Display menu - application parameters.
Bear in mind that estimated pump flow cannot be as precise as measured pump flow (from flow sensor) and therefore estimated pump may give total quantity with significant distortion.
One solution is to read estimated pump flow via PLC and calculate total quantity in PLC.
Other solution is to read SLFV by then PLC to return value by writing it into virtual input (e.g. AIV1). As ATV630 allows to assign pump sensor to virtual input, ATV630 will process it and hence total quantity will be calculated by the drive.
ATV630 needs real pressure sensor in order to estimate flow from H-Q curves. Pump curves must be configured in the drive. Virtual input to be assigned to installation flow and the rest is about the scaling.
Note that value in virtual input has different scaling than read SLFV, so you have to adjust it using virtual input scaling (AVxJ AVxK). Everything explained in attached picture. As an example psx config is attached.
Modbus TCP was used in example, but in principle any other communication is possible.
parameter FS1C that provides Total quantity will be visible also on HMI, in Display menu - application parameters.
Released for:Schneider Electric Australia
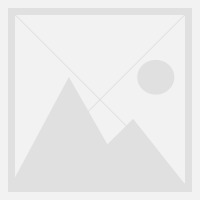
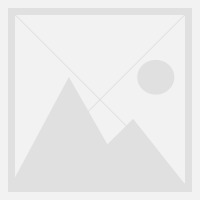