This FAQ has been written for NEAL (North East Africa and Levant) region. If you are looking for information for another region, please select the correct country from the top-left dropdown in the page and 'Navigate to Browse FAQs' in the Support menu.
Each device can detect its order in the chain of connected devices and assigns itself an address accordingly. This auto-addressing feature is provided by the terminal base backplane. In EcoStruxure Building Operation WorkStation, you create a logical I/O module to be associated with the physical I/O module on the I/O bus. You specify the I/O module type and name. Initially, the module ID is Null, which means that the I/O module is non-operational. You assign a module ID that is equal to the address (position) of the I/O module on the I/O bus. You can configure the module ID either when you create the logical I/O module or later. When the I/O module is plugged into the system at the intended position on the bus, the EcoStruxure Building Operation software automatically associates the physical I/O module with the logical I/O module that has a matching module ID and type.
I/O module address calculation
The backplane generates a 5-bit address corresponding to the order (position) of the terminal base in the chain and passes this address through the I/O bus to the
electronics module installed on the terminal base (base plate). The leftmost device in the chain gets the address (position) 1. The next device gets address 2, and so on, up to 32.

Each device can detect its order in the chain of connected devices and assigns itself an address accordingly. This auto-addressing feature is provided by the
terminal base backplane.
In EcoStruxure Building Operation WorkStation, you create a logical I/O module to be associated with the physical I/O module on the I/O bus. You specify the I/O module type and name. Initially, the module ID is Null, which means that the I/O module is non-operational. You assign a module ID that is equal to the address (position) of the I/O module on the I/O bus. You can configure the module ID either when you create the logical I/O module or later. When the I/O module is plugged into the system at the intended position on the bus, the EcoStruxure Building Operation software automatically associates the physical I/O module with the logical I/O module that has a matching module ID and type.
I/O module address calculation:
The backplane generates a 5-bit address corresponding to the order (position) of the terminal base in the chain and passes this address through the I/O bus to the electronics module installed on the terminal base (base plate). The leftmost device in the chain gets the address (position) 1. The next device gets address 2, and so on, up to 32.
NOTE: Position 1 is reserved for a power supply. Position 2 is reserved for a SmartX AS-P server or Automation Server. Although the power supply device gets an address, the PS-24V does not use it. When you replace an electronics module, the new module automatically picks up the same address. If you remove an electronics module from its terminal base, the addresses of the following devices are not affected.
I/O module address calculation
The backplane generates a 5-bit address corresponding to the order (position) of the terminal base in the chain and passes this address through the I/O bus to the
electronics module installed on the terminal base (base plate). The leftmost device in the chain gets the address (position) 1. The next device gets address 2, and so on, up to 32.
Each device can detect its order in the chain of connected devices and assigns itself an address accordingly. This auto-addressing feature is provided by the
terminal base backplane.
In EcoStruxure Building Operation WorkStation, you create a logical I/O module to be associated with the physical I/O module on the I/O bus. You specify the I/O module type and name. Initially, the module ID is Null, which means that the I/O module is non-operational. You assign a module ID that is equal to the address (position) of the I/O module on the I/O bus. You can configure the module ID either when you create the logical I/O module or later. When the I/O module is plugged into the system at the intended position on the bus, the EcoStruxure Building Operation software automatically associates the physical I/O module with the logical I/O module that has a matching module ID and type.
I/O module address calculation:
The backplane generates a 5-bit address corresponding to the order (position) of the terminal base in the chain and passes this address through the I/O bus to the electronics module installed on the terminal base (base plate). The leftmost device in the chain gets the address (position) 1. The next device gets address 2, and so on, up to 32.
NOTE: Position 1 is reserved for a power supply. Position 2 is reserved for a SmartX AS-P server or Automation Server. Although the power supply device gets an address, the PS-24V does not use it. When you replace an electronics module, the new module automatically picks up the same address. If you remove an electronics module from its terminal base, the addresses of the following devices are not affected.
Released for:Schneider Electric Egypt and North East Africa
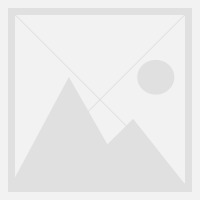
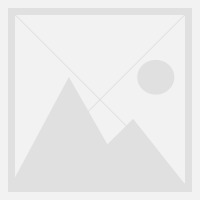