How to set up Schneider ATV21/212 drives for simple applications.
How to quickly test a drive
This test can serve as the first stage in a more complex commissioning process
Important clarification
Schneider supplies new drives with identical preset parameters.
This parameter set is called the ''Factory setting''
You can return to the factory settings at any time:
TYP = 3
This sheet assumes that:
The parameters are the factory settings (as with a new drive straight out of the box).
The motor to be driven is a traditional 50 Hz squirrel cage motor, not a synchronous or slip ring motor
The motor to be driven is the same rating as the drive
The setup engineer knows how to use the graphic display terminal or display (confirmation, tree structure)
1) To run the motor (one cable link and one parameter)
Set the SW4 switch to Source position
Set LL to the required speed reference (40 Hz for this example): AUF => LL = 40
Bridge terminal F (Run forward) to terminal P24
As soon as F is at the correct polarity, the drive starts immediately and reaches the 40 Hz speed reference as quickly as possible.
For reverse operation: ( note the reverse is not enabled as a factory default)
Set F112 to 3: F…. => F112 = 3 (Assigns R to run reverse)
Set F311 to 0: F…. => F311 = 0 (Enables forward and reverse operation)
Bridge terminal R to terminal P24
2) Run the motor with the acceleration and deceleration ramps (two cable links and one parameter)
Wiring
Bridge the PP terminals and AIV (10 volts to analogue input).
Switches
Set the SW3 switch to V (voltage): AIV is then a voltage input
Set the SW4 switch to Source: input F or R must be supplied by P24 (remember the R terminal is not assigned as reverse as default).
Parameter setting
Reset the LL parameter to the value 0: AUF menu => LL = 0 (not necessary if product is in factory settings).
Set the UL parameter to the required speed reference (40 Hz for this example) AUF menu => UL = 40.
Operation
Bridge the terminal F (Run forward) to terminal P24.
As soon as F is at the correct polarity, the drive starts and follows the acceleration ramp to get to its speed reference.
Remark: In the factory setting, depending on both its loads and current, the ATV21 drive can determine specific acceleration and deceleration ramps which are suitable in the majority of cases. Otherwise, it is possible to freeze the values of these ramps in the same way as with ATV11-31-71 drives
AUF menu => AU1 = 0 (default setting is 1)
AUF menu => ACC = acceleration ramp value
AUF menu => DEC = deceleration ramp value
3) Vary the speed with a potentiometer (wire up a potentiometer and a bridge)
Switches
- Set the SW3 switch to V (voltage): AIV is then a voltage input
- Set the SW4 switch to Source: input F, R must be supplied by P24 (remember the R terminal is not assigned as reverse as default).
Wiring
Use a potentiometer (standard SZ1RV1202 or a pot 2.2k Ohms to a max. of 10k Ohms) for the AIV analog input, wire the potentiometer complete resistor ( fixed resistance pins) between PP and CC and the midpoint (variable wiper) at AIV.
Parameter setting
- Reset the LL parameter to the value 0: see 1 to do this AUF => LL = 0 (not necessary if using factory settings).
- Settings for AIV parameters
§F201: Min.scale value of V - as a %
Example in 0-10V: This parameter must be set to 0 (0% of 10 V corresponds to 0 V)
In the factory setting it is on 0, therefore 0 V
§F203: Max.scale value of V - as a %
Example: 100 % = 10 V (factory setting)
§F202: Value in Hz at the analogue signal min.
For example, if you require 30 Hz at 0 V - this parameter should be set at 30 (factory setting at 0)
§F204: Value in Hz at the analogue signal max.
In the factory setting, this parameter is set to 50 Hz, therefore giving this frequency of 50 Hz at 10 V
Operation
- Bridge terminal F (Run forward) to terminal P24.
Once F has been activated, the drive starts and reaches its speed reference determined by the potentiometer. The speed can be changed with the potentiometer.
4) Motor thermal protection (one parameter)
- Set the drive thermal protection to protect the motor using the value from the motor rating plate, note the nominal current and enter it in the drive Ith parameter (tHR) on the 21 /212
AUF menu => tHR = Nominal Motor Currant
5) Optimisation/auto-tuning/Tun of the drive/motor unit (5 to 6 parameters)
Unlike the ATV11-ATV31-ATV61-ATV71 drives, auto-tuning is configured by F400, but is only actually performed on the first start command (F bridged).
AUF menu => uL = Nominal frequency indicated on motor rating plate
=> uLu = Nominal voltage indicated on motor rating plate
F … menu => F415 = Nominal current indicated on motor rating plate
=> F417 = Nominal speed indicated on motor rating plate
=> F400= 2.
Auto-tuning is performed when the first start command is given (F bridged). It lasts 3 seconds. During the auto-tuning process, the drive displays Atn1. If auto-tuning is successful: 0, or if it fails displays: Etn1. If it does fail then manually set F401, F402, F418, F419 to obtain the smoot and stable speed if the drive output is not stable
Released for:Schneider Electric Ireland
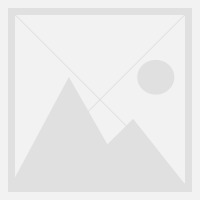
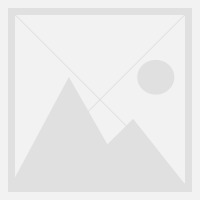