Details on SCF1:
Motor short circuit fault (hard detection)
Principle
The drive is protected against short circuit between the phase output and phase and phase to the ground.
When there is a short circuit, the inverter indicates the fault message SCF1.
It is a very quick (a few μs) hardware detection, the threshold is about 3 to 4 times of the nominal current of the inverter.
Probable causes
• There is a short circuit at the inverter output.
• Short circuit or earth fault in the motor or motor cable.
• Earth fault.
Remedies
• perform the diagnostic functions on the HMI, or SoMove service section.
• check the cables connecting the drive to the motor and the motor insulation.
Suggested methods: Please keep photo of the result of each step and prepare to share.
1. Check the cables connecting the drive to the motor, and the motor’s insulation
Using a 1,000V Megger, test the motor and leads
2. Check for tight wiring connections
3. Perform the Transistor test via the [DIAGNOSTICS] menu with the motor connected.
[Complete settings] [Maintenance] [Diagnostics]
Run [IGBT Diag w motor] IWT
4. Run the drive open circuit (with the motor disconnected, OPL turned off, and Motor Control Type set to V/F 5pts)
[Complete settings] [Error/Warning handling] [Output phase loss] -> set to 'No'
[Complete settings] [Motor parameters] -> set to 'V/F 5pts'
and check the drive's output (T) terminals for balanced voltages phase to phase
Run [IGBT Diag w/o motor] IWOT
5. Perform a diode check using terminals U/T1, W/T2, V/T3, PA+ and PC-.
NOTE: This step should be performed when no line voltage is present on the drive. Power down the drive before performing this step.
-Measure (using your meter's diode
scale) in one direction, then swap your leads and measure again
Measure between PA+ to T1, T2, and T3. Then swap leads and test again.
Next measure between PC- to T1,T2,T3 and then swap leads. (total of 12 measurements: 6 measurements to PA+ and 6 measurements to PC-)
-You should see 'OL' in one direction and a small voltage reading (approximately 0.3-.0.5V) in the other direction and each set of measurements should be consistent between phases.
-Values outside the acceptable range can indicate damage to the IGBT's or other components in the drive.

Motor short circuit fault (hard detection)
Principle
The drive is protected against short circuit between the phase output and phase and phase to the ground.
When there is a short circuit, the inverter indicates the fault message SCF1.
It is a very quick (a few μs) hardware detection, the threshold is about 3 to 4 times of the nominal current of the inverter.
Probable causes
• There is a short circuit at the inverter output.
• Short circuit or earth fault in the motor or motor cable.
• Earth fault.
Remedies
• perform the diagnostic functions on the HMI, or SoMove service section.
• check the cables connecting the drive to the motor and the motor insulation.
Suggested methods: Please keep photo of the result of each step and prepare to share.
1. Check the cables connecting the drive to the motor, and the motor’s insulation
Using a 1,000V Megger, test the motor and leads
2. Check for tight wiring connections
3. Perform the Transistor test via the [DIAGNOSTICS] menu with the motor connected.
[Complete settings] [Maintenance] [Diagnostics]
Run [IGBT Diag w motor] IWT
4. Run the drive open circuit (with the motor disconnected, OPL turned off, and Motor Control Type set to V/F 5pts)
[Complete settings] [Error/Warning handling] [Output phase loss] -> set to 'No'
[Complete settings] [Motor parameters] -> set to 'V/F 5pts'
and check the drive's output (T) terminals for balanced voltages phase to phase
Run [IGBT Diag w/o motor] IWOT
5. Perform a diode check using terminals U/T1, W/T2, V/T3, PA+ and PC-.
NOTE: This step should be performed when no line voltage is present on the drive. Power down the drive before performing this step.
-Measure (using your meter's diode
Measure between PA+ to T1, T2, and T3. Then swap leads and test again.
Next measure between PC- to T1,T2,T3 and then swap leads. (total of 12 measurements: 6 measurements to PA+ and 6 measurements to PC-)
-You should see 'OL' in one direction and a small voltage reading (approximately 0.3-.0.5V) in the other direction and each set of measurements should be consistent between phases.
-Values outside the acceptable range can indicate damage to the IGBT's or other components in the drive.
Released for:Schneider Electric New Zealand
Details on SCF1:
Motor short circuit fault (hard detection)
Principle
The drive is protected against short circuit between the phase output and phase and phase to the ground.
When there is a short circuit, the inverter indicates the fault message SCF1.
It is a very quick (a few μs) hardware detection, the threshold is about 3 to 4 times of the nominal current of the inverter.
Probable causes
• There is a short circuit at the inverter output.
• Short circuit or earth fault in the motor or motor cable.
• Earth fault.
Remedies
• perform the diagnostic functions on the HMI, or SoMove service section.
• check the cables connecting the drive to the motor and the motor insulation.
Suggested methods: Please keep photo of the result of each step and prepare to share.
1. Check the cables connecting the drive to the motor, and the motor’s insulation
Using a 1,000V Megger, test the motor and leads
2. Check for tight wiring connections
3. Perform the Transistor test via the [DIAGNOSTICS] menu with the motor connected.
[Complete settings] [Maintenance] [Diagnostics]
Run [IGBT Diag w motor] IWT
4. Run the drive open circuit (with the motor disconnected, OPL turned off, and Motor Control Type set to V/F 5pts)
[Complete settings] [Error/Warning handling] [Output phase loss] -> set to 'No'
[Complete settings] [Motor parameters] -> set to 'V/F 5pts'
and check the drive's output (T) terminals for balanced voltages phase to phase
Run [IGBT Diag w/o motor] IWOT
5. Perform a diode check using terminals U/T1, W/T2, V/T3, PA+ and PC-.
NOTE: This step should be performed when no line voltage is present on the drive. Power down the drive before performing this step.
-Measure (using your meter's diode
scale) in one direction, then swap your leads and measure again
Measure between PA+ to T1, T2, and T3. Then swap leads and test again.
Next measure between PC- to T1,T2,T3 and then swap leads. (total of 12 measurements: 6 measurements to PA+ and 6 measurements to PC-)
-You should see 'OL' in one direction and a small voltage reading (approximately 0.3-.0.5V) in the other direction and each set of measurements should be consistent between phases.
-Values outside the acceptable range can indicate damage to the IGBT's or other components in the drive.

Motor short circuit fault (hard detection)
Principle
The drive is protected against short circuit between the phase output and phase and phase to the ground.
When there is a short circuit, the inverter indicates the fault message SCF1.
It is a very quick (a few μs) hardware detection, the threshold is about 3 to 4 times of the nominal current of the inverter.
Probable causes
• There is a short circuit at the inverter output.
• Short circuit or earth fault in the motor or motor cable.
• Earth fault.
Remedies
• perform the diagnostic functions on the HMI, or SoMove service section.
• check the cables connecting the drive to the motor and the motor insulation.
Suggested methods: Please keep photo of the result of each step and prepare to share.
1. Check the cables connecting the drive to the motor, and the motor’s insulation
Using a 1,000V Megger, test the motor and leads
2. Check for tight wiring connections
3. Perform the Transistor test via the [DIAGNOSTICS] menu with the motor connected.
[Complete settings] [Maintenance] [Diagnostics]
Run [IGBT Diag w motor] IWT
4. Run the drive open circuit (with the motor disconnected, OPL turned off, and Motor Control Type set to V/F 5pts)
[Complete settings] [Error/Warning handling] [Output phase loss] -> set to 'No'
[Complete settings] [Motor parameters] -> set to 'V/F 5pts'
and check the drive's output (T) terminals for balanced voltages phase to phase
Run [IGBT Diag w/o motor] IWOT
5. Perform a diode check using terminals U/T1, W/T2, V/T3, PA+ and PC-.
NOTE: This step should be performed when no line voltage is present on the drive. Power down the drive before performing this step.
-Measure (using your meter's diode
Measure between PA+ to T1, T2, and T3. Then swap leads and test again.
Next measure between PC- to T1,T2,T3 and then swap leads. (total of 12 measurements: 6 measurements to PA+ and 6 measurements to PC-)
-You should see 'OL' in one direction and a small voltage reading (approximately 0.3-.0.5V) in the other direction and each set of measurements should be consistent between phases.
-Values outside the acceptable range can indicate damage to the IGBT's or other components in the drive.
Released for:Schneider Electric New Zealand
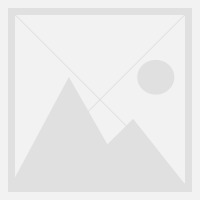
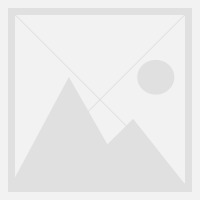
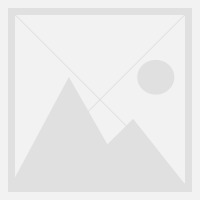
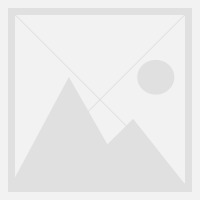
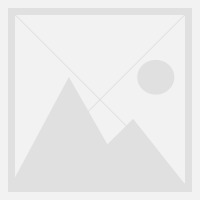
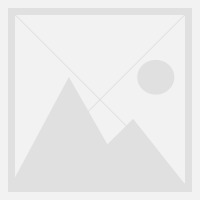
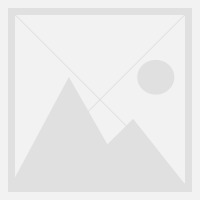
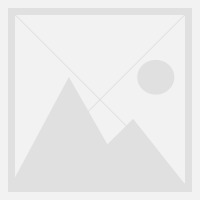