What is automation and how can an SME owner automate process?
The business world today operates on technology. This is undeniable even for companies who have been operating for decades or even hundreds of years. With technologies like the Internet-of-Things (IoT), Cloud, artificial intelligence (AI), business analytics, robotics and many more dominating business technology transformations today, how useful are these “automated processes” and “digital solutions”? How can an SME owner work with his or her plant managers and supervisors to review existing operations and drive a concerted effort to the positive acceptance and adoption of these modern solutions to automation?Steps the SME Owner Take to Plan, Implement and Monitor the Automated Process

One way to decide what exactly to automate is to invite different solution providers to sign a non-disclosure agreement (NDA), inspect the current processes you have and submit their recommendations and proposals on which areas require automation, how much they will cost, the impact they will have to your existing business and workforce, and how long they will take to plan, implement, test, retweak, maintain and upgrade. This way, the SME owner can review different proposals and consultations, preferably on an even comparison scale, to get a better range of what’s available, what’s acceptable and what’s financially doable before deciding if automating the entire chain or parts of it is critical for his or her business.
The planning stages are usually the longest and toughest, as proposal submissions, reviews, justifications, cost/benefit analysis and management buy-in and sign-offs are needed. But if planned and executed well, the rest of the implementation stages for automation should go smoothly, as long as monitoring and review systems are in place throughout each stage, and the company has the management buy-in to move things along.
Read Also: Did you know that Singapore SME owners can get up to 70% funding to automate their manufacturing business? Find out how to apply and receive government grants in our 17-page Government Automation Grant Guide.
It is thus safe to start small. Speak to your managers and identify a process or a step in the production that can benefit from automation. It not only allows you to get your team involved in the planning and implementation stage, but gives them the invested energy to be part of a transformative process that will ultimately benefit them in skills and mindset.
Whether the process is small or large, set some objectives for the automated process. They can include areas like:
- Accommodating timely production changes - Higher quality and consistency - Reduced costs - Greater capacity - Better time to market - Increased reputation as a value-added supplier - Improvements to safety and wellness in the work environment
There are also many automation-as-a-service providers, similar to software-as-a-service providers, which provide consultancy, projections, plans and are ready to make swift amendments down the line to accommodate any issues or changes along the way.

2. Always Plan Beyond Just the Automation Process: One critical step in adopting automation is to plan for growth in the implementation. While automating a process in a small way is good, what benefits, short-, medium- and long-term are there? Sometimes it’s better to ask the consultants to study your existing processes and give their projections. Other times, it’s better to consult your managers and factory floor operators to get the ground’s eye view on what they can possibly be. By the end of this exercise, ensure that there is a justification, with quantifiable and non-quantifiable, tangible and intangible targets and goals in mind. Set a clear period on how long the automation process experiment should take place, and measure its performance against past manual processes and future key performance indicators and goals.
- What are the Quantifiable Objectives of the Proposed Automation Plan? - What are the Non-Quantifiable Objectives? - Are the Objectives Tangible or Intangible? - For the Ones which are Intangible, What Sort of Measurement or Monitoring Processes will be set in place to Identify their Results?
Automation may come in the form of software services or hardware services. If you’re implementing automation that occupies factory floor space, always make projections for growth, especially if your business grows and demand increases, and you really need that immediate empty floor space for short- or medium-term operations.

3. Ensure There’s Post-Implementation Monitoring and Support: Another aspect of automation is the support and maintenance of the services. What are the warranties, spare parts availability and technical assistance the automation provider(s) will render to you when needed? What sort of pre-training is required for your engineers and operators, and whether there are certification courses they can take in being part of the automation process.
Note that even during the implementation of the automation process itself, there will more than likely be tweaking and fine-tuning. This is usually quite painful and tedious, as the solution provider has to work in line with the owner’s line managers to review, recalibrate and re-test the process. For example, if the owner runs a bottling plant, and the automated process of capping bottles shows some empty bottles being capped, then the owner will need the solution provider to calibrate the system, to figure out what’s wrong and fix the algorithm to ensure the process is correct. Then the cycle starts all over again.
There are normally several stages in the implementation and each stage is crucial. The sign-off for each stage, marked against a timeline of deliverables, is important. The SME owner must decide who among his or her line managers will be signing off on the stages of implementation, and ensure that these same line managers report directly to him or her should there be a delay in the sign-off due to recalibrations or re-tuning of the process. Delays normally translate into costs and unhappy customers, so ensure there are alert, remedy and rollback procedures during the implementation stage.
4. Ensure Access to Documentation and Secure Intellectual Property of Integrated Systems: Finally, review and note the intellectual property for systems developed for your automated process. If they are unique enough, you may want to consider having them documented and submitted as intellectual property. Other times, you may want to ensure that the third-party system integrator, who helped design, plan and implement the automated process and services, guarantees to keep your system confidential. This is to ensure that they do not resell the same unique design (or even share diagrams or drawings) they’ve consulted, built and sold to you, to your competitors (sometimes at a much lower cost).

There are many system integrators who can build and create such a system for SME owners, and these critical documentation are normally stored in the Cloud with two-factor authentication and privileged access management. Another reason why documentation of your automated process is critical, is for knowledge transfer and accountability.
There are many times when project managers and production line supervisors feign ignorance for not knowing a step in the process due to it being a new thing they’ve yet to learn and excel in. With documentation, the SME owner can ensure that everyone from the top-down has access to these steps and processes, and if in doubt, they should have the necessary access to review and reference them. If any of your line managers leave the company, the documentation and its steps will become even more critical, as you can then pass on the knowledge to new incoming managers, without the need to physically conduct extensive training for them or worse, expect them to learn these new automated process by instinct or past experience without supervision or guidance.
Conclusion
So there you have it, some points in helping the SME owner share and gain acceptance among his or her team on the need to explore automation, why the need for automation and how to begin automating at least a small step or process in a large environment of systems and procedures.This helpful guide serves to help SME owners on identifying what exactly they should automate, how they can kick start the process and what they should consider, from starting small, planning carefully especially with existing staff, setting quantifiable goals, to monitoring and measuring them, having remedy and rollback procedures, training staff and securing the integrated systems for future upgrades and competitive advantages as part of their overall post-implementation strategy.
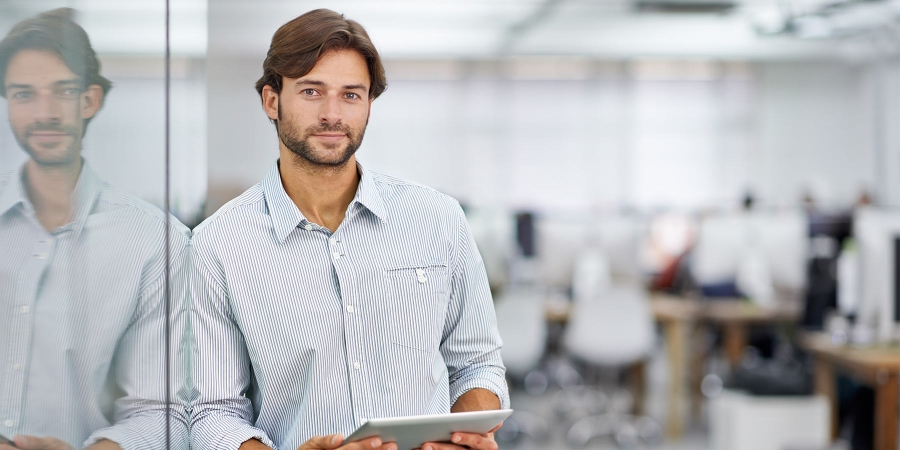
10 Major Challenges & the Benefits of Automation for Small Manufacturing Business Owners
Discover the 10 major challenges that small manufacturing business owners face and the benefits of automation.
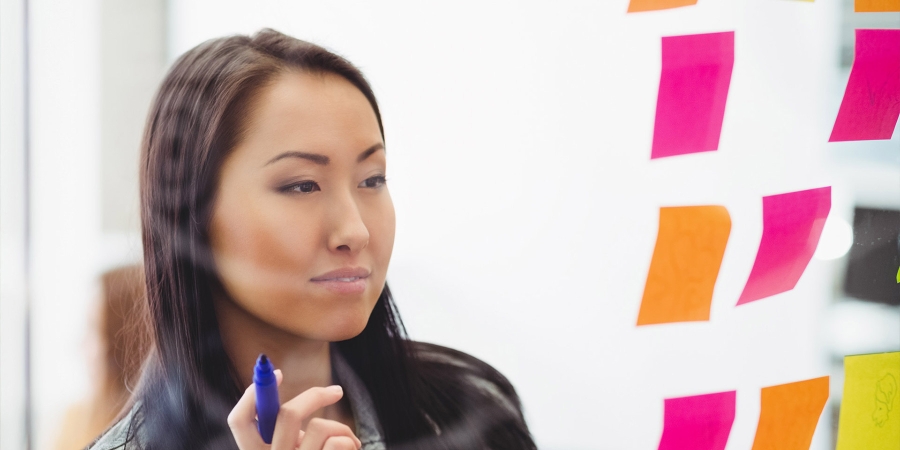
5 Lessons SMEs can learn from the COVID-19 crisis
The biggest lessons we can learn from this pandemic and what SME owners should do to take things in their stride.
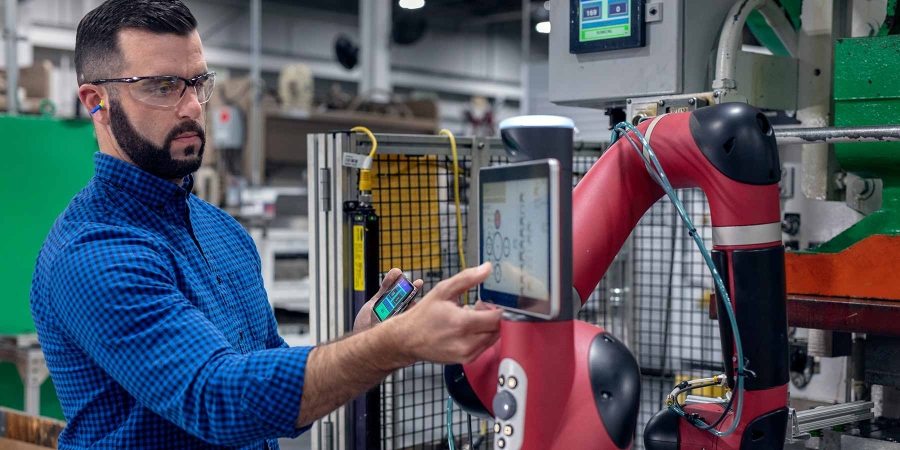
How to get the most out of your digitalisation dollar: Lessons from abroad
The key regional manufacturing trends in Southeast Asia and how Singapore SMEs can take these lessons on board to ride the wave.
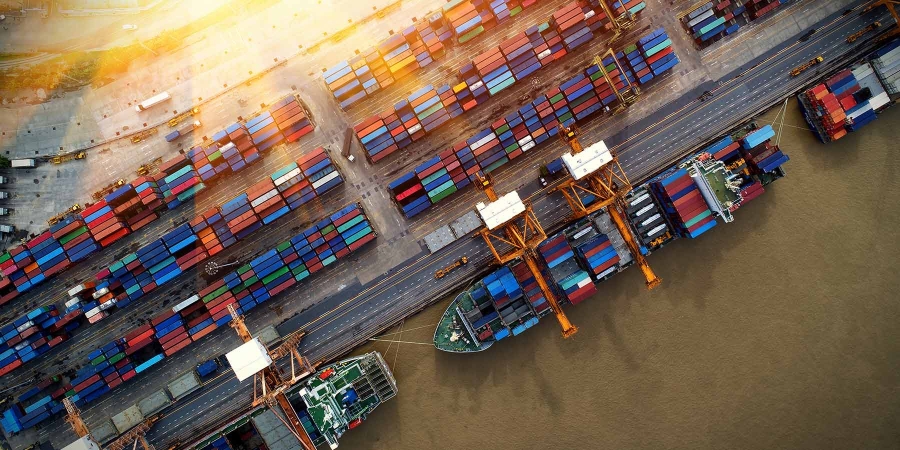
4 Tips on Building Manufacturing Agility for SMEs
Dr Ahmad Magad, Secretary-General of the Singapore Manufacturing Federation, shares with us the key mindset shifts that SME owners should adopt in order to build an agile and resilient organisation.
Need help?
Chat